マシニングセンタ(MC)とは?マシニングセンタの基礎を学ぶ!【滝本技研工業の樹脂加工作業マニュアル】
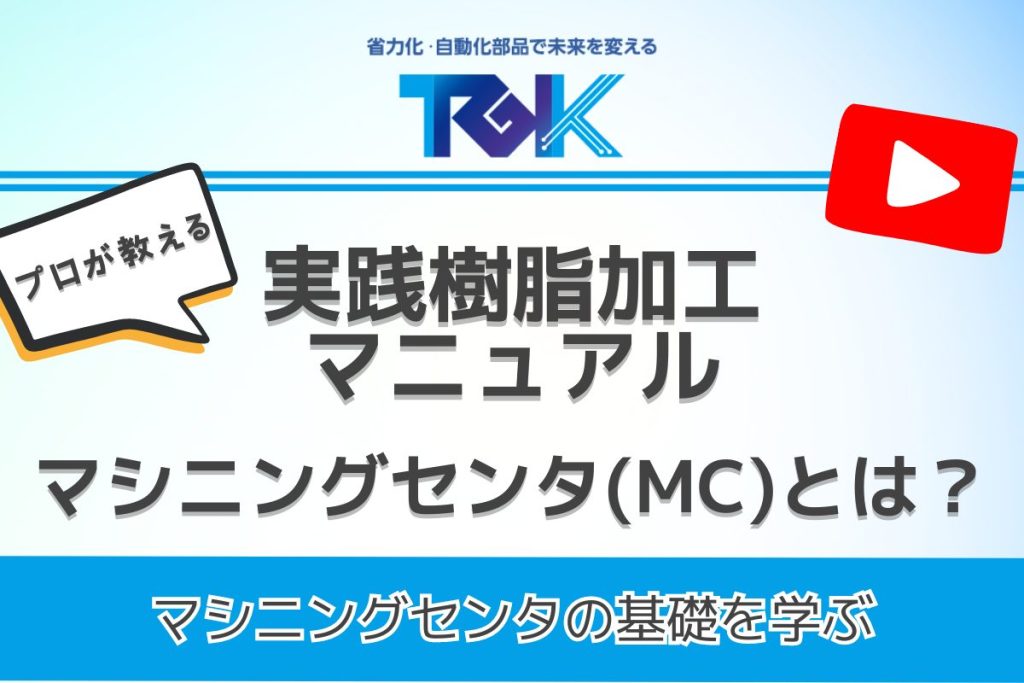
この記事は滝本技研工業公式YouTube「プラスチック・樹脂加工のプロ たきもとラボ」で公開している、プロが教える実践樹脂加工マニュアル動画を編集した記事となります。
実践樹脂加工マニュアル動画は再生リスト→プロが教える実践樹脂加工マニュアルから視聴することができます!
直線軸と座標系(右手の法則)
マシニングセンタの直線運動
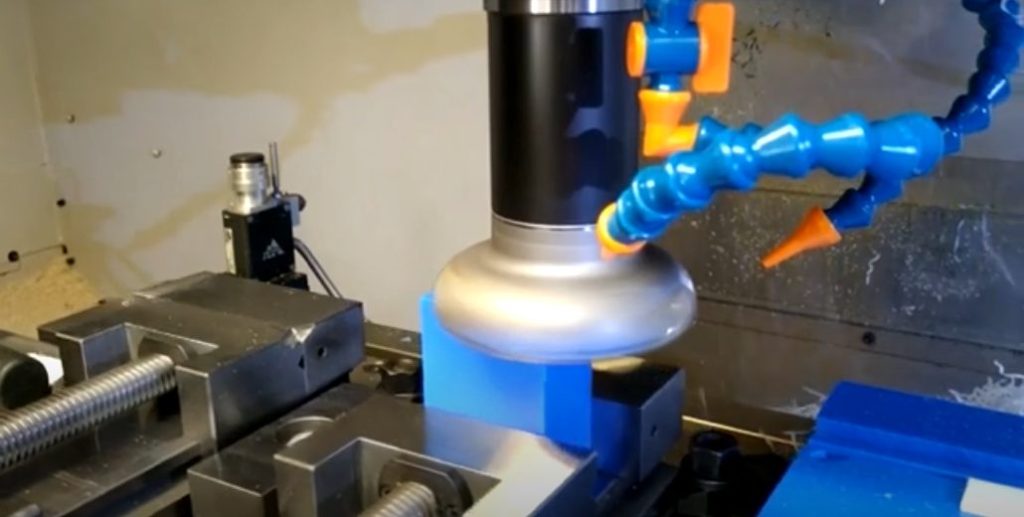
マシニングセンタは、座標値によって工具やテーブルを移動します。
移動には、座標系を理解する必要があります!
マシニングセンタの直線運動にはX、Y、Z軸があり、それぞれ左右、前後、上下を表します。
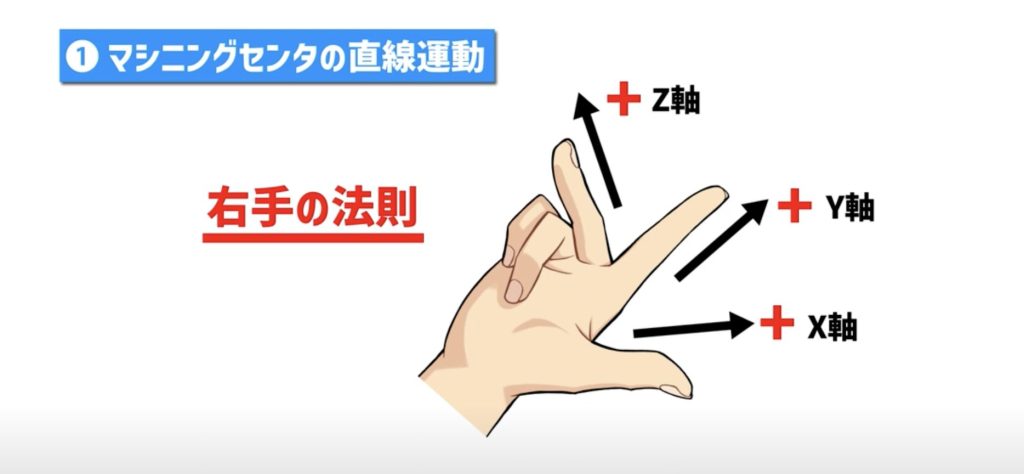
軸にはプラスとマイナスの向きがあり、右手の法則に従います。工作機械は主軸頭の動きを基準に、プラスとマイナスを判断します。
座標系の方向
縦型マシニングセンターは、一般的にX軸、Y軸、Z軸の3つの方向に動きます。テーブルがX軸とY軸方向に動く場合、各軸の正方向と負方向は、主軸の動きを基準にして決まります。
X軸のプラス方向は主軸頭に対して左であり、マイナス方向は右です。テーブルが左に移動すると、相対的に主軸が右に動いたことになるためです。
Y軸のプラス方向はテーブルがコラムの反対側に移動する方向でありマイナス方向は反対方向です。
座標系の向きは主軸頭の動きを基準に考えますが、主軸頭が固定されていてテーブルが動く場合、注意が必要!
座標系の方向がどちらに向くかはマシニングセンタを習得する際に最も混乱する点ですが慣れてしまえば問題ありません!頑張って習得しましょう!
マシンバイスで工作物を挟む際の注意点
強く掴まない
マシンバイスを使用して工作物を挟む際には強く締めすぎると工作物にストレスがかかり、歪みや浮きが生じる可能性があります…
弱すぎても工作物が動いてしまうため掴む力は切削力に耐えられる程度に設定する必要があります!
加工条件によって掴む力を調整し、荒加工時には強く、仕上げ加工時には弱くすることが望ましいです。この考え方は、押さえ金や旋盤加工のチャックでも同様!
マシンバイスの締め付け力と口金のたわみや平行度には関係があり、最も精度が安定する締め付け力が存在します。これらのことを覚えておくことが特に重要です!
マシンバイスを使用する際の工作物挟み方のポイント
工作物を直接テーブル上に設置する時の注意点
マシニングセンターでは、マシンバイスを使用せずに工作物を直接テーブル上に設置することがあります。
押さえ金を使用して工作物を固定しますが、その際に注意点がいくつかあります!
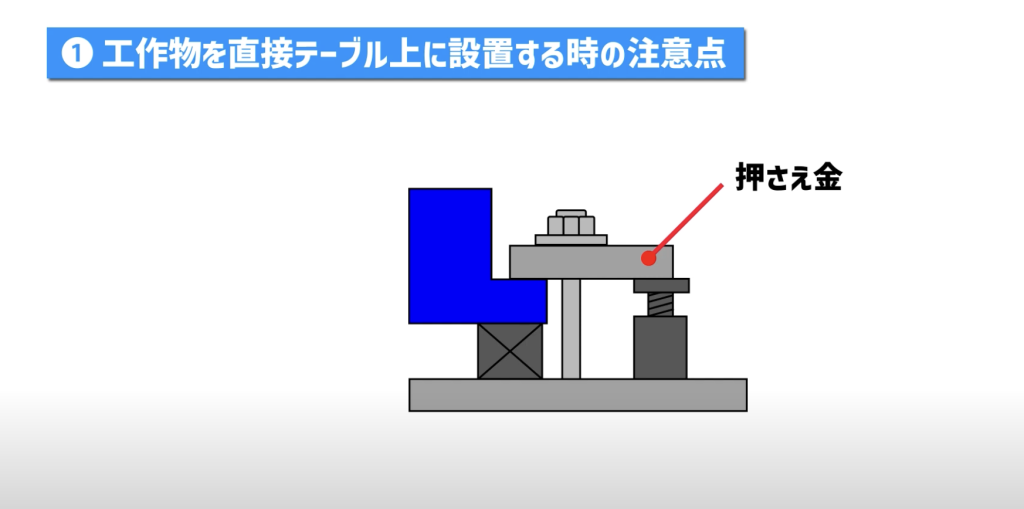
押さえ金の高さを調整するブロックを工作物と同じ高さに合わせ、押さえ金がテーブルと平行になるように取り付けます。出来ない場合は、少し高くなるように取り付けます。
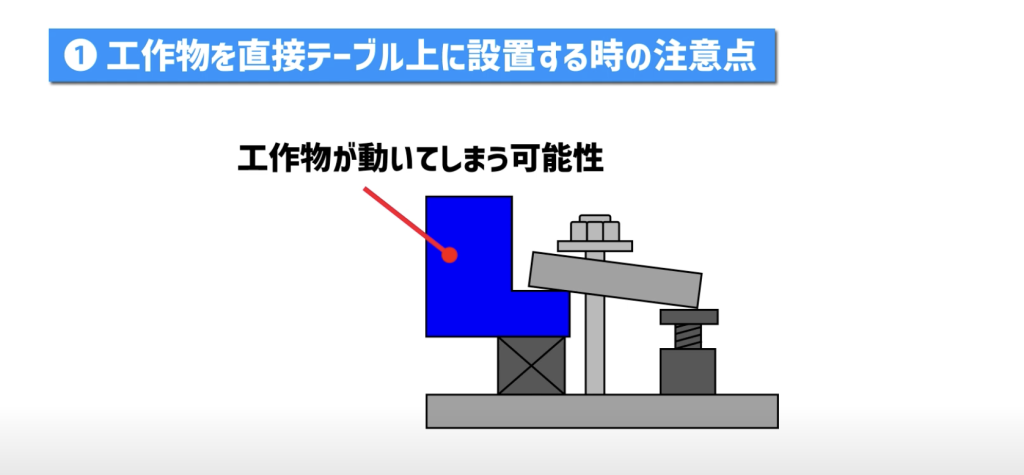
もし押さえ金の高さが工作物より高かったり、工作物やブロックが傾いていた場合には工作物の固定力が弱くなり、加工中に工作物が動いてしまう可能性があります。
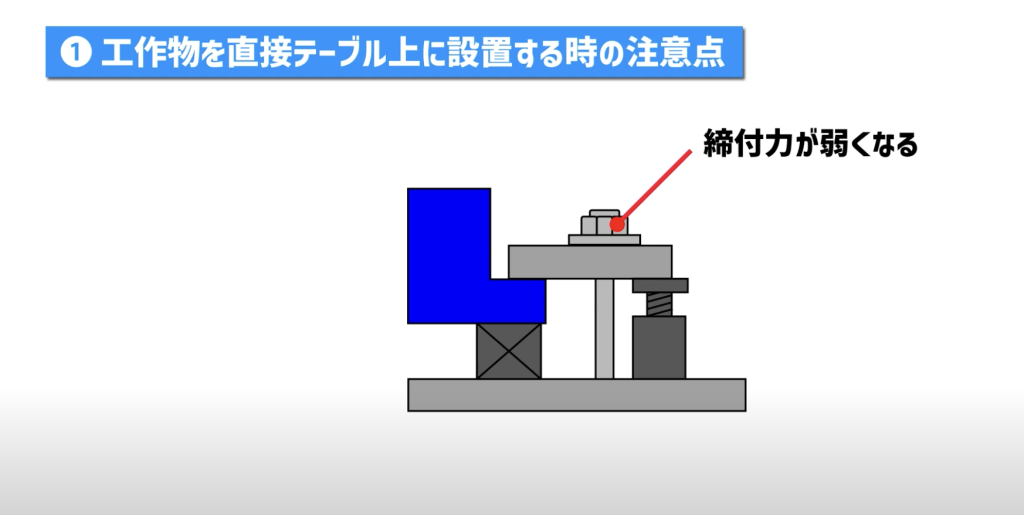
締付ボルトは工作物に近い側で締め付ける必要があります。締付ボルトの位置が離れるほど、締付力が弱くなり、工作物が動く恐れがあります。
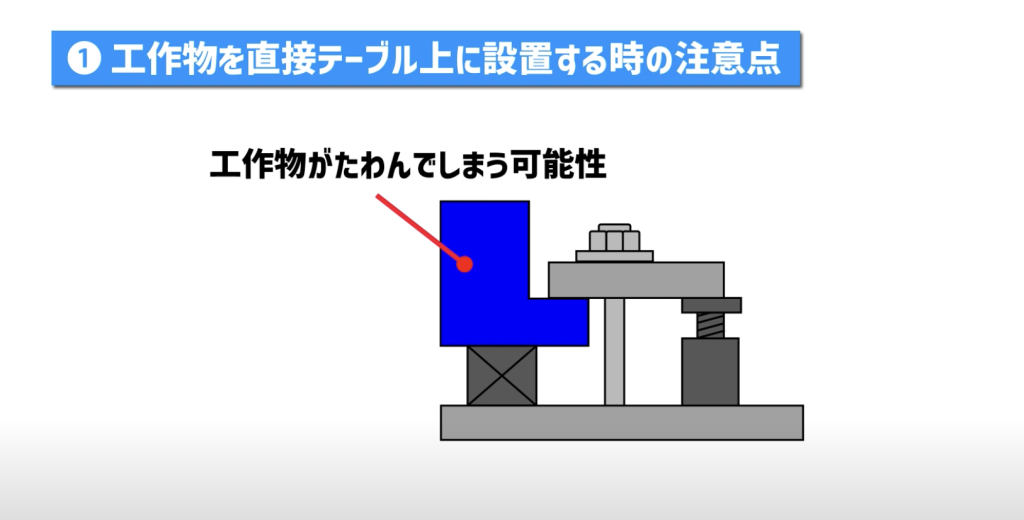
工作物をテーブルから浮かせている場合には平行台の位置と締め金の位置が一致していることが重要です。一致しない場合、工作物がたわんでしまう可能性があります。
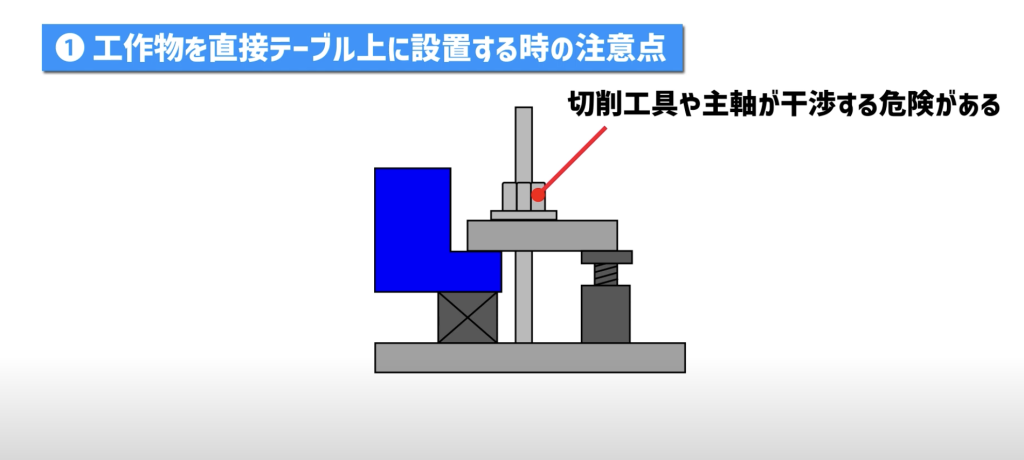
締付ボルトが長すぎると、切削工具や主軸が干渉する危険があるため、工作物の上面を超えない程度のものを使用する必要があります。
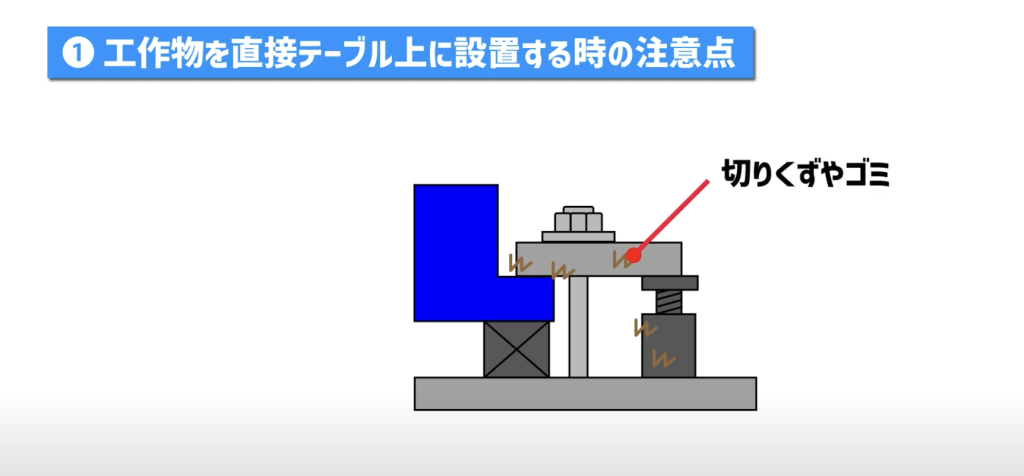
押さえ金が工作物にしっかりと被っていないと、確実な固定ができません
押さえ金と工作物の接触面に切りくずやゴミ、チリが堆積していると押さえ金が噛み込み、安定した固定ができなくなるため、清掃をしっかりしておく事が大切です!
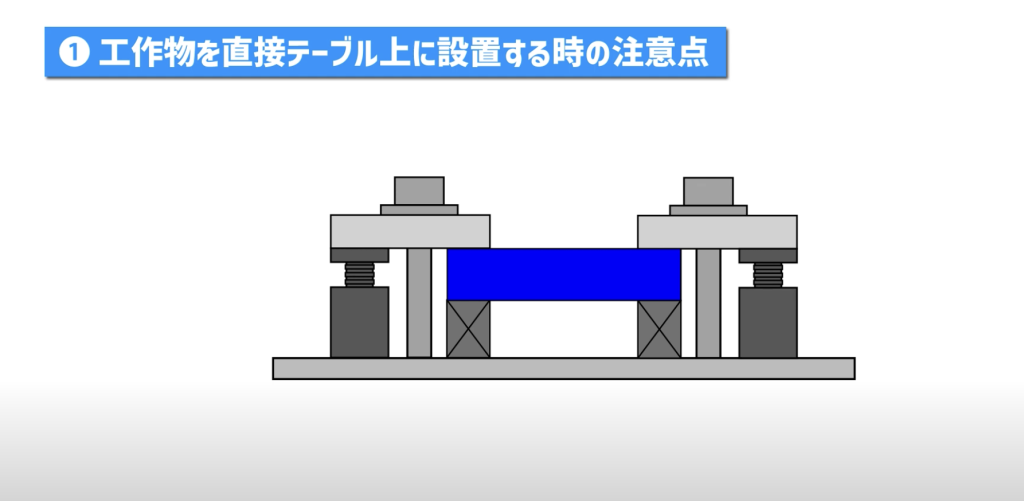
最後に、良い例を示して工作物の締め付ける高さと、押さえ金の高さが同じ高さであること押さえ金がテーブルと平行になっていることを確認し確実な取り付けを心がけるように注意してください!
工作物のチャッキング方法
工作物の固定方法
バイスは、工作物を固定する一般的な治工具であり、フライス盤に限らず様々な作業で使用されます。
バイスにはハンドルがあり、回すことで片側の口金が閉まり工作物を固定します。
工作物の形状には制限がなく、口金と工作物の間に鋼板やアルミ板を挟むことで傷をつけないようにすることもあります。
固定したバイスは、フライス盤のテーブルにボルトで固定しますが、工作物が薄い場合は加工したい面が口金に隠れてしまうため、パラレルブロックと呼ばれる2本の平行な台を使用してかさ上げします。
現場では”正直台”と呼ばれたりもします。
高精度の正直台は市販されており、焼き入れによってμmレベルの寸法精度が出ています。
これらのブロックは、工作物の加工精度に直接影響するため慎重に取り扱います。
テーブルに直接固定する方法
工作物が大きい場合は、バイスでは固定できないため、直接フライス盤のテーブルに固定します。
T溝を使ってハネクランプで固定する方法や、高さ調整が可能なステップクランプやステップブロックで固定する方法があります。
これらのクランプは一般に市販されています。
マシニングセンタによる工作物の取付精度と加工精度の追求
取付精度位の確認が必要
マシニングセンタでワークを加工する際に「マシンバイス」と呼ばれる固定具がよく使われます。
マシンバイスはテーブルに取り付けて使用しますが、その取り付け作業から加工精度の向上が始まります。
マシンバイスがX軸やY軸に対して傾いていると平行に加工することができず、底面とテーブルの間に切りくずやゴミが挟まっているとZ軸に対して傾いていると直角に加工することができません。
マシンバイスをテーブルに取り付ける作業やワークをマシンバイスに取り付ける作業の両方で取り付け精度を確認する必要があります。
マシニングセンタ加工では、段取り作業を含めて一つひとつ丁寧に作業を積み重ねることが加工精度の向上につながります。具体的には、ダイヤルゲージをスピンドルに取り付けマシンバイスの固定側口金やワークを設置する摺動面に押し当てて、取り付け精度を確認します。
ワークをマシンバイスに取り付けた際にも、ダイヤルゲージをワークの上面や側面に押し当てて取り付け精度を確認します。
加工前には必ず自分でマシンバイスが平行であり、直角に取り付けられているかを確認し他人に任せずに自分で行うことが重要です。
他人に任せることは加工精度を犠牲にすることと同じです。
フライス加工の特徴
フライス盤の種類
「フライス」という言葉は、 多数の切削刃を備えた工具全般を指し、それを使う加工機械を「フライス盤」と呼びます。
フライス盤は英語では「ミーリングマシン」とも呼ばれ、以下のような加工が可能です。
フライス盤の種類
- 平面加工(フェースミーリング) :工作物の平面を広く平面に削る加工
- 側面加工(エンドミル):側面加工、段付きの形状、円弧などの加工が可能
- 溝加工(エンドミル、スリットカッター、メタルソー):溝形状、ポケット状のくぼみ、キー溝、スリットなどを加工することができる
- 穴あけ加工(ドリル、リーマ、エンドミル):旋盤やボール盤と同様に、フライス盤でも穴加工が可能
- 曲面加工(ボールエンドミル):複雑な曲面加工は、NCフライス盤やマシニングセンタで行われる
フライス盤は旋盤とは異なり、工具を回転させて削ります。
工具は回転のみで、工作物を前後左右上下に動かして、所定の形状に削る原理により加工が行われます。
加工条件は工具の「回転数」と工作物への「切込み量」と「送り速度」の3つになります。
タップ加工の特異性と使い分ける切削タップの種類
タップ加工は失敗した際のリスクが大きい
タップ加工は通常、工程の最後に行われるため、失敗すると大きなリスクがあります。
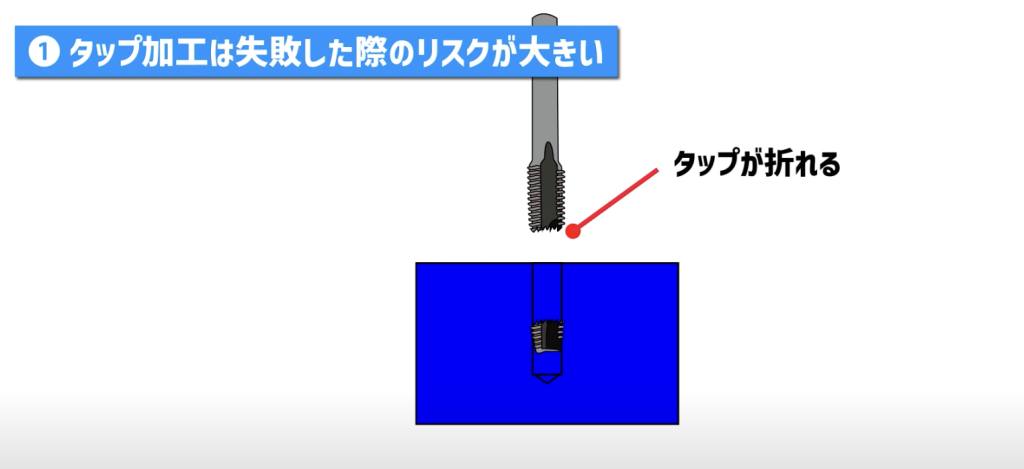
タップが折れてしまうと、工作物に取り残されたタップを取り除くことが困難で修復に多大な時間がかかる場合があります。
修復できない場合は不適合品となり、再度製造しなければなりません。
正面フライスやエンドミルの切削条件は回転数、送り速度、切り込み深さの3つですが、タップ加工では送り速度はピッチに依存しているため、作業者は調整できません。
タップは軸方向に加工されるため、切り込み深さの概念はありません。
タップ加工は正面フライスやエンドミル、ドリルと比べて加工ミスのリスクが高い一方で、切削条件の調整が回転数の1つのみという難しい加工です。
タップの選択は非常に重要です。
切削タップの種類
タップには、切削タップと非切削タップの2種類があります。
切削タップには溝があり、切削油剤の供給や切りくずの排出を担っています。
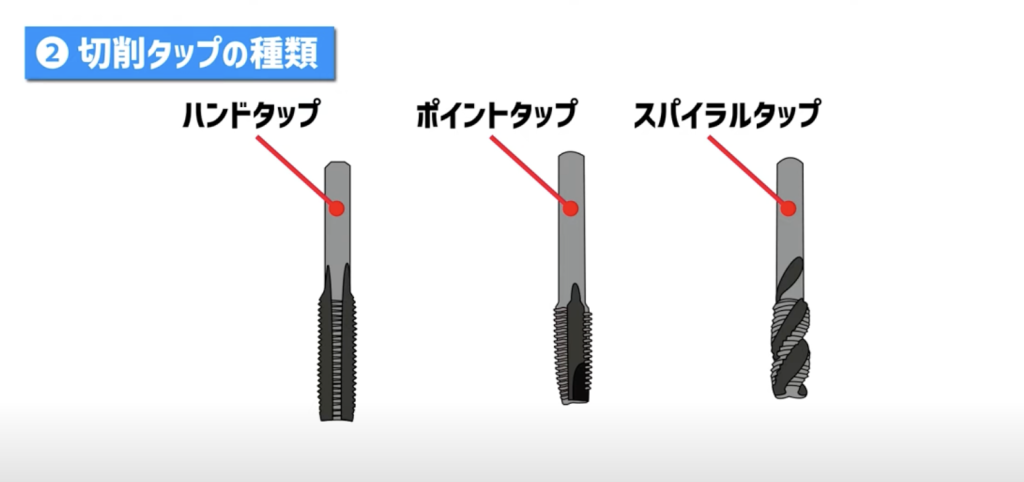
生産現場では、ハンドタップ、ポイントタップ、スパイラルタップの3種類がよく使われています。
ハンドタップは最も一般的で7~10山の山数を持つものを「さきタップ」、3~5山を持つものを「中タップ」、1~3山を持つものを「上げタップ」と呼びます。
ポイントタップは、直線状のみぞに数山分だけ斜めに削り取られた溝を持ち、切りくずを進行方向に押し出すように設計されています。また、ポイントタップは切りくずを進行方向に押し出すため、通り穴には適していますが、止まり穴には使用できません。
スパイラルタップは溝がドリルのようにねじれており、切りくずが溝に沿ってシャンク方向に押し出されるため、止まり穴に適しています。切れ刃が溝を通る切りくずを噛み込みやすく、切削トルクが大きく、折れやすいという欠点があります。
スパイラルタップは、右ねじれと左ねじれの2種類がありますが、左ねじれの場合、切りくずが進行方向に排出されるため、止まり穴には使用できません。
表面粗さの種類(Ra、Rz、三角記号)
表面粗さの指標
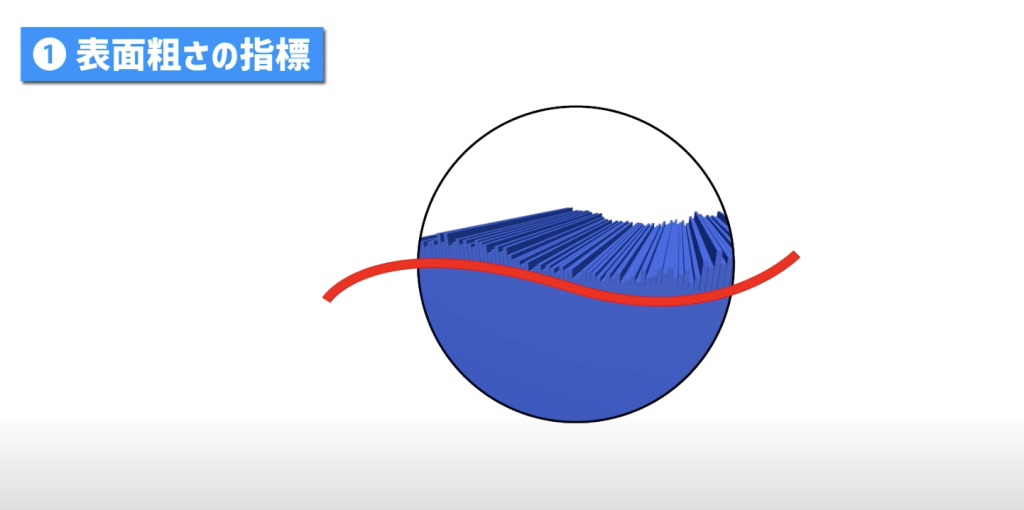
工作物をマシニングセンタで加工すると、切削工具による凹凸が表面に生じます。
この微小な凹凸を「表面粗さ」と呼び現在の機械図面では算術平均粗さと最大高さ粗さの2つの指標で表記されます。
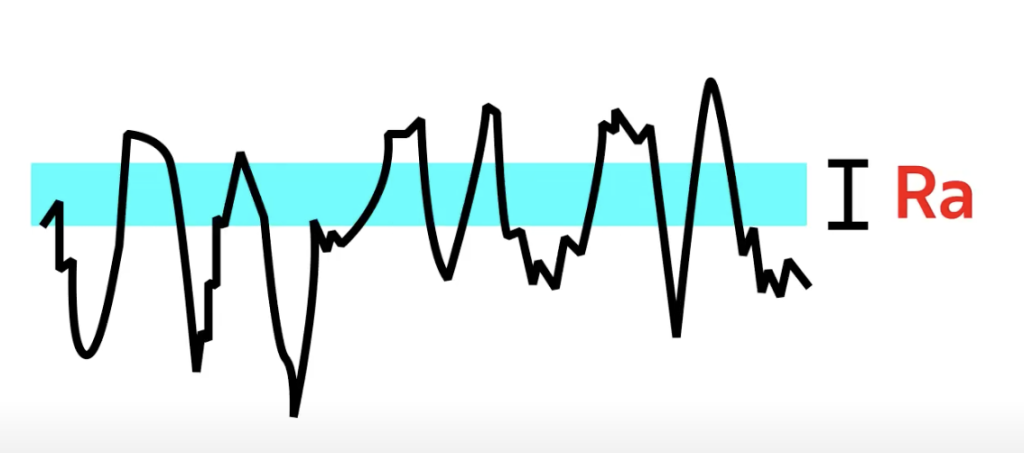
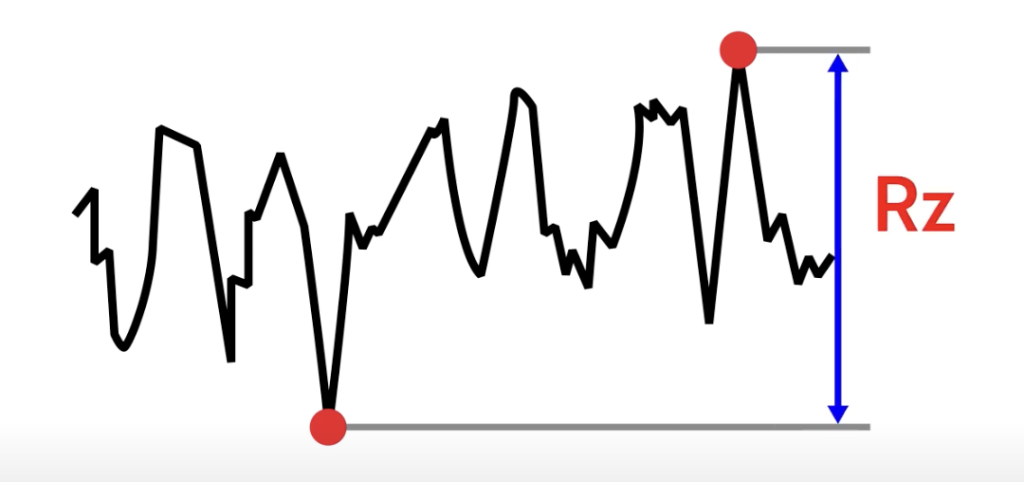
算術平均粗さは凹凸を面積として捉え、平均的な高さの値を示し、最大高さ粗さは最も高い山から最も低い谷までの差を表します。
三角記号 | 算術平均粗さ (Ra) | 最大高さ粗さ (Rz) |
---|---|---|
▼ | 25 12.5 | 100 50 |
▼▼ | 6.3 3.2 | 25 12.5 |
▼▼▼ | 1.6 0.8 0.4 | 6.3 3.2 1.6 |
▼▼▼▼ | 0.2 0.1 0.05 0.025 | 0.8 0.4 0.2 0.1 |
表面粗さを指標化する際には、かつては三角記号が使用されていましたが、現在は算術平均粗さと最大高さ粗さがよく用いられます。
三角記号には1つから4つまで4段階あり、算術平均粗さと最大高さ粗さには11段階あります。
三角記号が多くなるほど表面粗さは小さくなり、より滑らかな表面になります。
表面粗さを指標化する方法が変更されたのは工業製品の機能が進化するに伴い、より細分化された指標が必要とされたためです。
三角記号は具体的な数値による分類ではなかったため、数値による指標が必要とされました。
このような背景から、現在の表面粗さの指標は算術平均粗さと最大高さ粗さに変更されました。
算術平均粗さを4倍すると最大高さ粗さに相当するという関係がありますが、4倍にならない場合もあるので参考程度にしてください
FAQ
樹脂加工と金属加工では何が違いますか?
樹脂は熱に弱く、加工時に変形しやすいため、切削条件やクランプ方法が金属とは異なります。たとえば樹脂ではバイス跡が残らないよう治具が重要!
樹脂加工でおすすめの工具はありますか?
超硬エンドミルやアルミ用の高送りエンドミルが推奨!摩耗が少なく、切削熱も抑えられます。
樹脂加工時に切削条件はどう設定すべきですか?
金属よりも回転数を上げ、送りは控えめに設定するのが基本です。使用する樹脂の種類によって異なるため、加工テストで最適条件を確認してください!
樹脂加工における注意点は?
静電気、変形、反り、バリの発生などが挙げられます。冷却エアブローや仮止めの工夫、研磨工程の追加で対処可能です。
マシニングセンタでの樹脂加工時におすすめのクランプ方法は?
ソフトジョーや専用の吸着治具を使うことで、クランプ痕を防止できます。クッション材を挟むのも効果的!
滝本技研工業の豊富な素材&カット販売


樹脂は量販売がない…でも少量だけほしい…
滝本技研工業ではそんなお困りごとの声をお聞きして、 樹脂素材のカット販売をしています!必要な量のみを購入することでコストダウンにも繋がります!
また、常時1000万円分の在庫がありますので「ちょっとレアかも?」な材料でもご用意できる可能性がありますので、素材でお困りの方は滝本技研工業にお任せください!
お問い合わせ
見積もり、お問い合わせはこちらから!
FAXお見積もり用紙はこちら